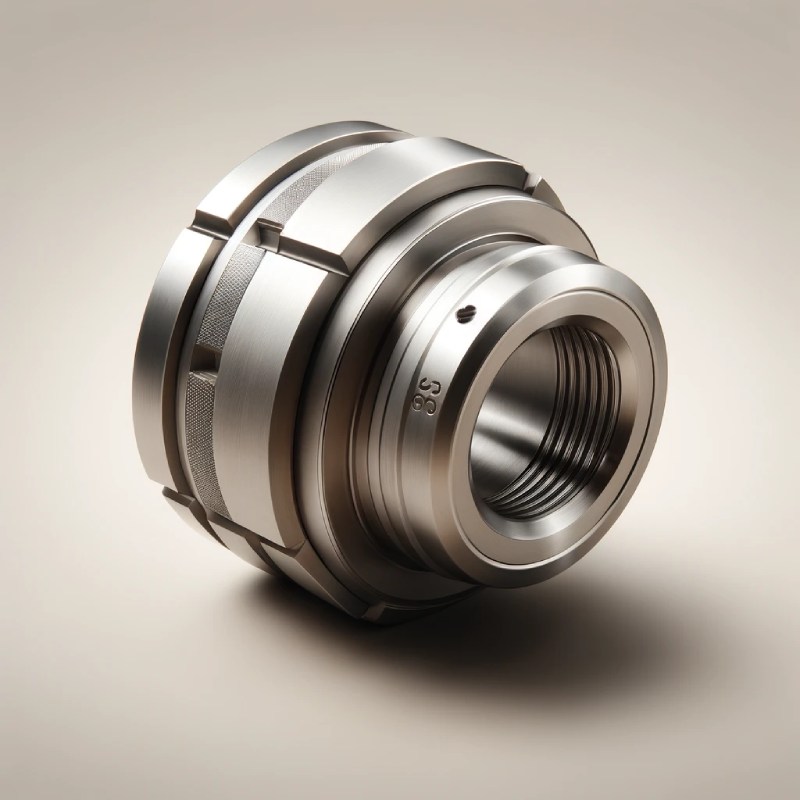
- Introduction
- Metals Suitable for CNC Machining
- Aluminum
- Stainless Steel
- Mild Steels
- Alloy Steel
- Brass
- Copper
- Titanium
- Comparison Tables
- How to Select Metallic Material for CNC Machining
- Factors for Selecting a Metal Material for CNC Machining
- Conclusion
- The Komacut Advantage
- FAQs
Choosing the appropriate metal for CNC machining is crucial, as it influences both the cost-effectiveness and performance of your project. By adhering to the principles discussed in this article, you can steer clear of common mistakes and make well-informed choices, ensuring you select the optimal material for your CNC-machined metal components.
Introduction
One of the primary challenges in metal selection for CNC machining is that not all metals are suitable for a particular process. Some metals, such as hardened steels, require longer machining times and higher costs due to their increased hardness. While materials, like cast iron, are not easily machined and may require specialized tools and techniques. This can significantly impact production schedules and budgetary constraints, add complexity to the machining process, and lead to suboptimal results.
The cost and performance ramifications of selecting the wrong material are significant. Choosing an unsuitable material can escalate scrap rates, extend lead times, and increase overall production costs. Additionally, it can produce parts that fail to meet required specifications, resulting in quality issues and customer dissatisfaction.
Fig. 1: Sheet Metal Materials
Metals Suitable for CNC Machining
Metals are widely used in CNC machining for their strength, durability, and versatility. Understanding the properties and characteristics of common metals used in CNC machining is essential for selecting the right material for a given application.
Aluminum
Aluminum is a lightweight, corrosion-resistant metal with good mechanical properties. It is available in various grades, each offering specific properties tailored to different applications.
Fig. 2: Aluminum Parts
Aluminum Alloy | Description | Yield Strength (MPa) | Tensile Strength (MPa) | Hardness (Brinell) |
---|---|---|---|---|
Aluminum 6061 | Widely used for its balanced strength-to-weight ratio and excellent machinability. | ≥276 | ≥260 | HV 15 - 18 |
Aluminum 6082 | Similar to 6061, more prevalent in Europe due to compliance with British Standards. | 85 to 320 | 140 to 340 | 40 to 95 |
Aluminum 7075 | Exceptional fatigue properties. Can be heat treated to high strength and hardness, rivaling certain steels. Often used in aerospace applications. | ≥503 | ≥572 | HB 150 ±5 |
Aluminum 5083 | Higher strength compared to other aluminum alloys. Remarkable resistance to seawater, ideal for marine uses. Well-suited for welding. Ideal for construction uses. | ≥270 | ≥340 | HB 75 |
Table 1: Overview of Common Aluminum Alloys and Their Properties
Applications
- Aircraft frames, engine parts, and structural elements with precise tolerances and exceptional durability.
- Automotive engine components, transmission cases, and structural supports.
- Heat sinks, housings, and components with efficient thermal management and excellent thermal conductivity.
- Surgical instruments, prosthetics, and diagnostic equipment, emphasizing biocompatibility and resistance to sterilization.
- Components of consumer goods, sports equipment, and household appliances, for aesthetic appeal, strength, and lightweight.
Properties
- Low Density - aluminum has a density approximately one-third that of steel, making it ideal for applications where weight reduction is critical.
- High Strength-to-Weight Ratio.
- High Corrosion Resistanceas it forms a protective oxide layer on its surface, which prevents further oxidation and provides excellent resistance to corrosion.
- Good thermal conductivity.
- High Electrical Conductivity.Although not as conductive as copper, aluminum is still a good conductor of electricity and is used in electrical applications where weight is a consideration.
- Non-magnetic, which is advantageous in applications where magnetic interference needs to be minimized.
- Does not produce sparks when struck, making it suitable for use in explosive or flammable environments
- High reflectivity for both light and heat, making it useful in applications such as light fixtures and thermal insulation.
- It is 100% recyclable without losing its properties, making it an environmentally friendly material choice
- Biocompatible - Aluminum is generally biocompatible and is used in medical devices and implants.
Additional Advantages
- Aluminum alloys are highly favored in various industries due to their exceptional strength-to-weight ratio, excellent thermal and electrical conductivity, and innate resistance to corrosion.
- While aluminum alloys generally exhibit lower strength and hardness compared to steel, they can be anodized to form a durable, protective surface layer.
- Aluminum alloys are also prized for their machinability and cost-effectiveness, particularly in bulk production and prototyping.
Stainless Steel
Stainless steel is a versatile and widely used material known for its excellent properties.
Fig. 3: Steel Part from Komaspec
Applications
- In the automotive sector, stainless steel is used for exhaust systems, trim, and structural components. Its ability to withstand high temperatures and resist corrosion makes it ideal for these applications.
- The aerospace industry uses stainless steel for various components including fasteners, landing gear, and aircraft frames. Its strength and resistance to extreme temperatures and corrosion are crucial for aerospace applications.
- Stainless steel is preferred for medical instruments, surgical tools, and implants due to its biocompatibility and ease of sterilization. It is also used in pharmaceutical processing equipment.
- Used in marine environments for boat fittings, propellers, and desalination plants due to its excellent resistance to saltwater corrosion.
- Stainless steel is common in components used for household and commercial appliances due to its corrosion resistance, food-safe qualities, and ease of maintenance.
Here are some of the key properties of stainless steel:
- Corrosion Resistance – very high due to the presence of chromium, which forms a passive layer of chromium oxide on the surface, preventing further oxidation.
- High tensile strength, making it suitable for applications that require robust and durable materials.
- Thermal Stability - Can withstand high temperatures without losing its strength or experiencing significant deformation, making it ideal for applications involving heat exposure.
- Aesthetics- The smooth, shiny finish of stainless steel makes it an attractive choice for architectural and decorative applications.
- Food Safe- It is easy to clean and does not support the growth of bacteria and other pathogens, making it a preferred material in the food, medical, and pharmaceutical industries.
- 100% recyclable, which makes it an environmentally friendly material choice.
- Magnetism - Some stainless steels are magnetic (such as those in the martensitic and ferritic families), while others are not (such as those in the austenitic family).
- Impact Resistance - Exhibits excellent impact resistance, which is crucial for applications subjected to mechanical stress and impact.
- High Wear Resistance, contributing to its longevity in applications involving abrasion and mechanical wear.
- Maintains its toughness even at cryogenic temperatures, which makes it suitable for use in extreme environments.
- Resists a wide range of chemicals and acids, making it ideal for use in chemical processing industries.
These properties make stainless steel a highly versatile material, used in a wide range of applications including construction, automotive, aerospace, medical devices, food processing equipment, and consumer products.
Stainless Steel Grade | Description | Key Properties | Applications | Yield (MPa) | Tensile (MPa) | Hardness |
---|---|---|---|---|---|---|
Stainless Steel 304 | The most common stainless steel alloy, excellent for general use. |
|
| ≥205 | ≥520 | HB 76 – 187 |
Stainless Steel 316 | Higher corrosion resistance than 304, especially against chlorides like seawater. |
|
| ≥205 | ≥520 | HB 76 – 187 |
Stainless Steel 2205 Duplex | Superior strength and corrosion resistance, used in challenging environments. |
|
| ≥448 | ≥620 | 31 HRC |
Stainless Steel 303 | Exceptional machinability, slightly less corrosion resistant than 304. |
|
| ≥241 (annealed), ≥414 (cold worked) | ≥620 (annealed), ≥690 (cold worked) | HB 163 (annealed), 229 (cold worked) |
Stainless Steel 17-4 (SAE grade 630) | High strength, can be heat treated, excellent for rigorous applications. |
|
| ≥1070 | ≥1240 | 33-43 HRC |
Table 2: Comprehensive Guide to Stainless Steel Grades: Properties and Applications
Mild Steels
Mild steels, also known as low-carbon steels, are valued for their good mechanical properties, high machinability, and weldability.
Applications
- Structural steel in buildings and bridges.
- Machinery parts and equipment.
- Nails, screws, and bolts.
- Cookware and kitchen utensils (though less common due to rusting).
Properties
- Easily welded and formed into various shapes.
- Decent strength, though not as high as high-carbon steels or other alloys.
- Mild steel is ferromagnetic, meaning it can be magnetized.
- Relatively inexpensive compared to other types of steel.
- Ease of machinability as it can be machined using common methods.
- Prone to rust if not properly protected, limiting its use in corrosive environments without surface treatment.
Additional advantage
- Mild steel is cost-effective and has wide application in various industries for general purposes such as in jigs and fixtures.
- It is prone to corrosion and chemical damage.
Here are a few types of mild steels available:
- Mild Steel 1018:This is a general-purpose alloy known for its good machinability and weldability. It also boasts excellent toughness, strength, and hardness, making it the most commonly used mild steel alloy.
- Mild Steel 1045:Classified as medium carbon steel, it offers good weldability, machinability, and high strength, along with impact resistance.
- Mild Steel A36:This is a common structural steel with good weldability, suitable for various industrial and construction applications.
Alloy Steel
Alloy steel is a steel alloy with added elements such as chromium, nickel, and molybdenum to enhance its mechanical properties. It offers high strength, hardness, and wear resistance, making it suitable for CNC machining applications requiring durability and toughness.
Applications
- Automotive components such as gears, axles, crankshafts etc.
- Oil and gas industry (drill collars, pipelines, valves).
- Aerospace components like landing gear, and turbine blades.
- Bearings and springs.
- Structural components in enclosures and products
- Surgical instruments and medical devices.
Properties
- Alloying elements like chromium, nickel, and molybdenum increase the strength of steel.
- Increased hardness, making alloy steels suitable for wear-resistant applications.
- Improved toughness, making the steel less brittle and more resistant to fracturing under stress.
- Certain alloying elements, like chromium, impart corrosion resistance to alloy steels.
- Some alloy steels retain their strength and hardness at high temperatures, making them suitable for high-temperature applications.
- Alloy steels are often used in applications requiring resistance to abrasion and wear.
- Alloy steels can vary in their weldability, with some requiring pre- or post-weld heat treatment for optimal properties.
Additional advantage
- Alloy steels have better mechanical properties compared to mild steels, due to additional alloying elements.
- These alloys exhibit improved hardness, toughness, fatigue, and wear resistance, making them crucial in various industrial applications.
Here are common alloy steels:
- Alloy steel 4140: is prized for its favorable mechanical properties, including good strength and toughness. It finds utility in a wide range of industrial applications. However, due to its composition, it is not recommended for welding.
- Alloy steel 4340:is a highly versatile material. It can be heat treated to achieve high levels of strength and hardness, while still maintaining good toughness, wear resistance, and fatigue strength. it is weldable, offering flexibility in manufacturing processes.
Brass
Brass is an alloy of copper and zinc, known for its excellent machinability, corrosion resistance, excellent electrical conductivity, and attractive golden color. It is commonly used in CNC machining for applications such as fittings, valves, and musical instruments due to its aesthetic appeal and ease of machining.
Fig. 4: Brass Brick
Applications
- Electrical connectors and terminals.
- Radiator cores and tanks.
- Marine hardware (due to its corrosion resistance).
- Fasteners and hardware (screws, bolts, nuts).
- Bearings and gears.
- Ammunition casings.
Properties
- Excellent resistance to corrosion, especially from seawater and other saline environments.
- Easily shaped and formed into various components.
- Good thermal conductivity, making it useful in heat exchangers and radiators.
- Better electrical conductivity than many other alloys, though less than pure copper.
- Inherent ability to kill bacteria, beneficial for use in surfaces and medical instruments, though the speed and efficacy depends on copper content
- Good resistance to wear and fatigue, useful for mechanical applications.
- Highly machinable.
- Non-magnetic.
Copper
Copper is a soft, malleable metal with excellent electrical and thermal conductivity. Ideal for electrical components, such as connectors, busbars, and conductive springs. Its thermal conductivity is also high, making it suitable for heat exchangers and other applications where efficient heat transfer is crucial.
Fig. 5: Pipe Connector Made of Copper
Applications
- Electrical wiring and cables.
- Plumbing pipes and fittings.
- Heat exchangers and radiators.
- Electrical connectors and circuit boards.
- Renewable energy systems (solar panels, wind turbines).
- Components that require an antimicrobial surface for use in healthcare or public spaces.
Properties
- Excellent electrical conductivity which is second only to silver.
- High thermal conductivity makes it efficient at conducting heat, and useful in heat exchangers and cookware.
- Resists corrosion in various environments, particularly in atmospheric and seawater.
- Excellent machinability.
- Naturally kills bacteria/microbes, beneficial for healthcare and public spaces.
- Good resistance to wear and fatigue.
- Highly recyclable without loss of properties.
- Non-Magnetic.
- The density of pure copper is approximately 8.96 g/cm³.
Additional advantage
- In CNC machining, copper can be machined into various shapes and sizes with high precision, allowing for the creation of complex parts with tight tolerances.
- Its compatibility with various finishing techniques, such as plating, polishing, and coating, further enhances its versatility and aesthetic appeal.
Titanium
Titanium has unique properties, making it highly sought after in various industries. Its lightweight nature, coupled with its remarkable strength-to-weight ratio, makes it ideal for applications where weight reduction is critical.
Fig. 6: Titanium Brick
Applications
- Aerospace components and accessories due to titanium's high strength and low weight.
- Surgical instruments, implants, and prosthetics.
- Automotive parts like exhaust systems, valve components, and suspension springs.
- Marine applications that require high strength, lightweight, and corrosion resistance - underwater fastenersand hull components.
- Components for oil and gas, power generation, and other heavy industries where strength, durability, and resistance to extreme conditions are essential.
Properties
- High strength-to-weight ratio.
- Excellent corrosion resistance.
- High melting point about 1,668°C
- Biocompatibility (non-toxic and not rejected by the body).
- Good fatigue resistance.
- Low thermal and electrical conductivity compared to other metals.
- Difficult to machine.
- High cost.
Comparison of Mechanical Properties
Metal | Grade | Strength | Hardness | Machinability | Density (g/cm³) |
---|---|---|---|---|---|
Mild Steel | AISI 1018 | Medium | Medium | High | 7.85 |
Brass | C36000 | Medium | Medium | High | 8.4-8.7 |
Copper | C11000 | Low | Low | Low | 8.96 |
Aluminum | 6061-T6 | Medium | Medium | High | 2.70 |
Alloy Steel | 4140 | High | Medium | Medium | 7.85 |
Alloy Steel | 4340 | High | Medium | Medium | 7.85 |
Stainless Steel | 304 | Medium | Medium | Medium | 8.00 |
Stainless Steel | 316 | Medium | Medium | Medium | 8.00 |
Titanium | Grade 5 (Ti-6Al-4V) | High | High | Low | 4.5 |
Table 3: Comparison of Mechanical Properties
Comparison of Functional Properties
Metal | Electric Conduction | Heat Resistance | Magnetic | Chemical Resistance | Corrosion Resistance | Cost | Applications |
---|---|---|---|---|---|---|---|
Mild Steel | Low | Low | Yes | Low | Low | Low | Construction, automotive, general engineering |
Brass | Medium | Low | No | Medium | Medium | Medium | Plumbing, electrical connectors, decorative items |
Copper | Very High | Low | No | Low | Low | Medium | Electrical wiring, electronics, heat exchangers |
Aluminum | High | Low | No | Low | Medium | Low | Aerospace, packaging, construction |
Alloy Steel 4140 | Low | Medium | Yes | Medium | Medium | Medium | Automotive, machinery, tool making |
Alloy Steel 4340 | Low | Medium | Yes | Medium | Medium | Medium | Aerospace, automotive, high-stress components |
Stainless Steel 304 | Low | Medium | No | High | High | High | Food processing, chemical equipment, kitchenware |
Stainless Steel 316 | Low | Medium | No | High | High | High | Marine applications, chemical processing, medical devices |
Titanium Grade 5 | Low | High | No | High | High | Very High | Aerospace, medical implants, marine environments |
Table 4: Comparison of Functional Properties
How to Select Metallic Material for CNC Machining
Selecting the right metallic material for CNC machining is a critical decision that can impact the performance, cost, and quality of the final product. Several factors need to be considered when choosing a material:
1. Consider the Part Type
- Is it a bushing, an enclosure, a shaft, a gear?
- What are the characteristics of this type of part? Does it need to be smooth and frictionless, or is strength the priority?
2. Consider Part Use
- Determine the specific requirements of the part, including mechanical properties (strength, hardness, etc.), dimensional tolerances, surface finish Etc.
3. Consider the application
- Does your target application have any special requirements for the parts in terms of electrical conductivity, magnetism, etc.?
- What kind of environment is the application – is it highly corrosive? Is there a high degree of exposure to UV or weathering? High heat?
- Are there regulatory or certification requirements?
4. Finalize Requirements & Selection Criteria
- Based on the product and application requirements, establish criteria for selecting the metal, alloy, and grade, considering factors such as machinability, cost, availability, and suitability for the application.
5. Shortlist Material Options
Shortlist your potential materials and then evaluate trade-offs between material properties, cost factors, and application requirements.
- Consult References: Refer to material selection guides, handbooks, and databases to compare the properties of different metals and grades and their suitability for CNC machining.
- Cost Analysis: Compare the cost of each material, including raw material cost, machining costs, and any additional costs (e.g., surface treatment, post-machining operations).
- Final Selection: Based on the above considerations, select the metallic material that best meets the requirements for the CNC machining process.
Factors for Selecting a Metal Material for CNC Machining
Material Properties
- Tensile strength, yield strength, hardness, and ductility are important mechanical properties.
- Higher tensile strength and hardness are desirable for parts subjected to high loads
- Ductility is important for parts that require deformation without breaking.
Thermal Properties
Thermal conductivity and coefficient of thermal expansion are important for parts subjected to temperature variations.
High thermal conductivity helps in dissipating heat generated during machining, while a low coefficient of thermal expansion ensures dimensional stability at different temperatures.
Thermal Expansion - The rate at which a material expands when heated is critical in maintaining the precision and tolerance of CNC machined parts. Metals with a low coefficient of thermal expansion are preferred for applications where dimensional stability is crucial, as they will not deform significantly with temperature changes, ensuring the parts remain within specified tolerances.
Chemical Properties
Corrosion resistance and chemical compatibility are crucial for parts exposed to corrosive environments or chemicals. Materials like stainless steel and certain plastics offer excellent corrosion resistance, making them suitable for such applications.
Machinability
Factors such as material machinability, complexity of the part, and tool wear affect machining time. Materials that are easy to machine, such as brass or aluminum, may result in shorter machining times compared to harder materials like titanium or stainless steel.
Costs
Cost-effectiveness in material selection involves evaluating the cost per kilogram of material and the machining time required to produce the part.Some materials may have a higher initial cost but offer cost savings in terms of longer tool life or reduced machining time.
Fig. 7: Factors for Selecting a Metal Material for CNC Machining
Application Needs
Selecting materials based on the operational environment and final product requirements involves considering the following important factors:
Property | Materials | Applications |
---|---|---|
Corrosion Resistance | Stainless Steel, Brass | Suitable for applications in corrosive environments. |
Electrical Conductivity | Copper, Aluminum | Used for electrical components and conductive housings. |
Food Grade | Stainless Steel, Aluminum | Selected for applications in food processing or medical industries. |
Part Needs | Varies | Consideration of specific part requirements like wear resistance, weight, and hardness. |
Wear Resistance | Alloy Steels | Suitable for parts subjected to wear, such as gears and bushings. |
Weight | Aluminum | Selected for applications where weight is a critical factor. |
Hardness | Tool Steels, Certain Alloys | Suitable for parts requiring high wear resistance and durability. |
Table 5: Key Material Properties and Their Applications
Conclusion
Selecting the right metal material involves a step by step consideration of the application, the part type and geometry, and the final performance required. The good news is that by following our guidelines, and with the right feedback from your machining supplier, highlighting the best options aren’t as difficult as it appears.
The Komacut Advantage
Many companies struggle to find reliable and cost-effective suppliers for low and medium-volume production – prototyping companies charge high set-up costs and per-piece pricing; larger manufacturers are not interested in orders of several hundred or even thousand pieces. Not to mention the time and expertise needed to manage and coordinate with these suppliers. Komacut is a solution to bridge the gap between prototyping and mass production, with instant quotes, easy management, and flawless execution from quote to order to delivery.
For more information on designing and manufacturing CNC machiningand machined parts, please visit the Komacut website. Instant quotations and design feedback, a range of materials, engineering design guidelines, and more - visit Komacut today for superior CNC machining solutions.
FAQs
How does machinability affect metal selection for CNC machining?
Machinability refers to how easily a material can be cut, shaped, and finished. Metals with high machinability require less cutting force, generate less heat, and produce better surface finishes, making them more cost-effective and efficient for CNC machining.
What are some common metals used in CNC machining?
Common metals used in CNC machining include aluminum, steel, stainless steel, brass, and titanium. Each metal offers unique properties that make it suitable for different applications. Aluminum is known for its lightweight and excellent machinability, while steel provides high strength and durability.
Why is aluminum often preferred for CNC machining projects?
Aluminum is often preferred for CNC machining projects due to its excellent machinability, lightweight nature, corrosion resistance, and ability to be anodized for enhanced surface properties. Its versatility and cost-effectiveness make it a popular choice across various industries.
What are the benefits of using stainless steel in CNC machining?
Stainless steel offers several benefits for CNC machining, including high strength, excellent corrosion resistance, and good heat resistance. These properties make it ideal for applications requiring durability and exposure to harsh environments, such as aerospace, medical, and marine industries.
How does the hardness of a metal impact CNC machining?
The hardness of metal impacts the tool wear, cutting speed, and surface finish during CNC machining. Harder metals can cause more rapid tool wear and require slower cutting speeds, while softer metals are easier to machine but may require additional considerations for maintaining dimensional accuracy.
Are there specific metals recommended for high-precision CNC machining?
For high-precision CNC machining, metals like aluminum, brass, and certain grades of stainless steel are often recommended. These metals offer excellent machinability, allowing for tight tolerances and fine surface finishes, which are essential for high-precision applications.
What are some challenges associated with machining titanium?
A.Machining titanium presents challenges such as high tool wear, and low thermal conductivity. These factors require specialized tooling, cooling techniques, and careful control of machining parameters to achieve optimal results.
How can surface treatments impact the performance of CNC-machined metal parts?
Surface treatments, such as anodizing, plating, and heat treating, can significantly enhance the performance of CNC-machined metal parts by improving properties like corrosion resistance, hardness, and wear resistance. These treatments extend the lifespan and functionality of the parts in their intended applications. Finishes like zinc plating can enhance the wear resistance of a part in a moving application, while a finish which is more vulnerable to scratching or wear will do the opposite – this is why powder coating and e-coating aren’t used on parts which will be exposed to significant wear.
Why is it important to consider the grain structure of metals in CNC machining?
The grain structure of metals influences their mechanical properties and machinability. Fine-grained metals typically exhibit higher strength and better surface finish, while coarse-grained metals might be more prone to cracking or deformation during machining.
What considerations are necessary for selecting metals for medical device manufacturing via CNC machining?
For medical device manufacturing, the primary concern is the same as other applications: choosing a material which fits the strength, cost and other considerations of that particular part. There is an additional complication in that metal for medical applications often must meet stringent biocompatibility standards. Materials like titanium and certain stainless steel grades are preferred for their non-reactivity with bodily tissues, high corrosion resistance, and ability to be sterilized without degrading.
How does surface roughness affect the functionality of CNC-machined metal parts?
Surface roughness impacts the performance of CNC-machined parts, affecting factors like friction, wear, and sealing capability. Achieving the desired surface finish is critical for ensuring that parts function correctly in their intended applications, particularly in high-precision or high-stress environments.
How do I balance cost and performance when selecting a material?
Evaluate the material's cost against its performance benefits. Sometimes a higher-cost material can offer better durability or lower machining costs in the long run. Consider total lifecycle costs and the specific needs of your application.